Michael Heidler is a German author who has written a couple very well-researched books on German weaponry, including a massively comprehensive catalog of manufacturing codes which we reviewed a little while back. Mr. Heidler is working on a book on German Volkssturm weapons, and has sent us a sample in the form of an article on the prototype Volkspistole made by Walther (we also have a video on the Mauser Volkspistol, courtesy of the Pattern Room). So without further ado:
The German late-war Walther Volkspistole
by Michael Heidler
The most common pistol of the German Wehrmacht was the Walther P38 in caliber 9 mm. Their serial production began in 1939 by Walther, followed by Mauser (1941) and Spreewerk (1943). The model P38 was thought to replace the expensive and time-consuming manufactured standard pistol model P08. But due to the circumstances of the war this plan could not be implemented completely: In the first half of the year 1944 the German troops lost 110,092 handguns and this number rose to 282,701 handguns in the second half of the year. Such high losses could not even be compensated by all three manufacturers together.
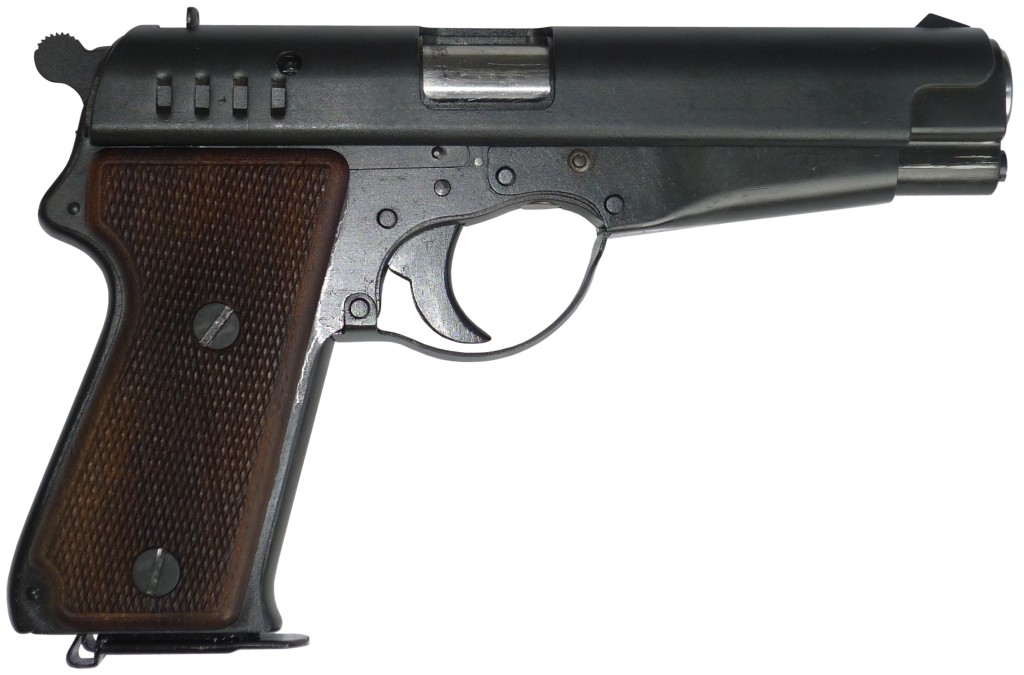
The shortage of handguns had unforeseen consequences for the German Volkssturm (people’s storm), when the first units should get equipped in late 1944. Although the Gauleiter were authorized to receive weapons from armament factories in their districts, these weapons had to come from over-production or had to be made after an official Army contract had ran out. But this claim was only written on paper. The manufacturers had their hands full even to take care of all official orders. At the end of the day there was nothing left for the Volkssturm.
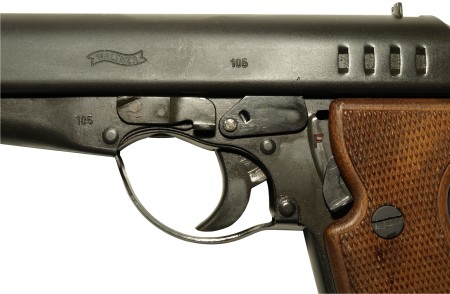
Since early 1944, Walther and Mauser tried to simplify their weapons and to develop new models. None of them went into serial production, but the gained experience benefited the companies when the call for a “people’s pistol” came up at the end of the year. Now it was necessary to produce more faster and cheaper than ever before. In addition, the weapon had to use the P38 magazines and to hit a 20x20cm target on 25 meters.
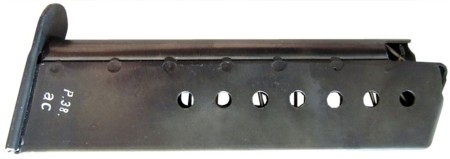
On November 30, 1944 there was a meeting between the Haupt-Dienststellenleiter Saur, SS-Obergruppenführer Gottlob Berger and other members of the Technisches Amt (Technical Department). In the process Saur got the promise for a monthly supply of 20,000 “Volkspistolen (people pistols) model Walther”. At the very next day, Berger sent an official contract to SS-Standartenführer and Wehrwirtschaftsführer (leader of defense economy) Erich Purucker, who in turn forwarded it to the Walther company. There the order was accepted as “War-Order Nr.1005 Waffen SS” on January 4, 1945.
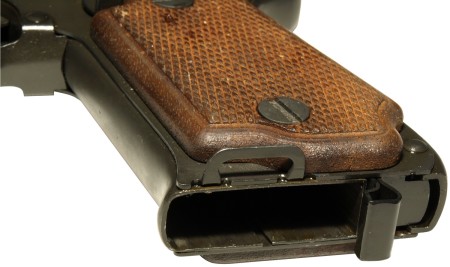
For Walther it was hard to cope with this additional order. The production was already quite busy with the production of P38, K43, VG1 and other military equipment. Also it was getting more and more difficult to acquire all the necessary raw materials to keep the production. So director Fritz Walther wrote a letter to Purucker on January 24, 1945:
“I confirm the receipt of the above-mentioned war-order. In the meantime a decree of the OKH (Wa A Az. 72-b-35 Wa Chef Ing 4 VIa2) for procuring raw materials and supply and an order for setting up a production facility for the Volkspistole (handwritten added: 9 mm) have arrived. […] Serial production is not possible before the production facility is set up. The compulsory dates of delivery February 1945, March 1945 etc. can not be confirmed. The raw materials request to the Hauptausschuß Waffen (Main Committee for Weapons) in Berlin is released today. Please influence the Committee to allocate the required supply-rights for iron and sheet metal as quickly as possible. The order SS-4924 is classified as Dringlichkeitsstufe I (precedence rating level 1). My other productions run in the precedence rating level 0 and I have all sorts of difficulties in obtaining the raw material. And therefore I fear that the procurement of raw materials for the lower level 1 is considerably more difficult“.
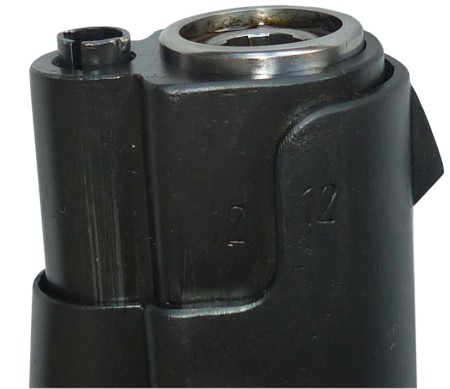
As a result of this letter, Walter received a message on February 10, that the order is now classified as the highest level called “Führer-Notprogramm” (Führer emergency program). However, it remains questionable whether this had been of some use. The few surviving pistols do not suggest the start of a large-scale serial production. And on 4th April the U.S. Army occupied the Zella-Mehlis area.
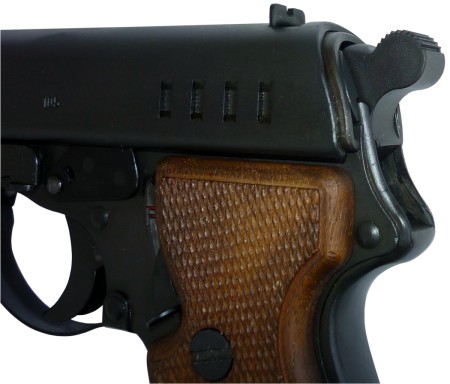
In the absence of significant documents not much can be found out about the simplification experiments with the P38. However, a few experimental pieces have survived the war and show the way to the people’s pistol “Volkspistole”. The two different simplified models are similar to the American Colt 1911 and were especially used for testing stamped sheet metal parts. Other innovations such as a rotating barrel can not be found on the Volkspistole any more.

The real Volkspistole looks similar to these experimental pistols from the outward appearance, but it is only a conventional single action weapon with blowback mechanism. Almost the whole gun is made of stamped sheet metal, except for barrel, bolt-head, springs, grip-plates and a few other small parts. Almost everything is joined together with bolts and rivets, and the spot-welded points have been reduced to a minimum. Only the wooden grip-plates are still attached with common screws. The weight of the complete gun is 1.086 kg.
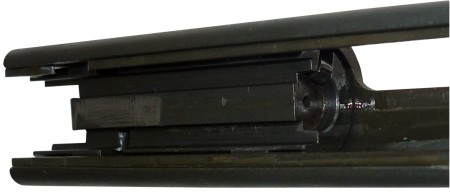
The whole range of simplification becomes obvious when disassembling the Volkspistole: The barrel is retained in the frame by a hardened cylindrical plug which engages the blind hole shown in the underside of the barrel breech. When lowering the lever on the left side of the frame above the trigger, the plug retracts and the barrel can be withdrawn forward. Afterwards the slide can be removed.
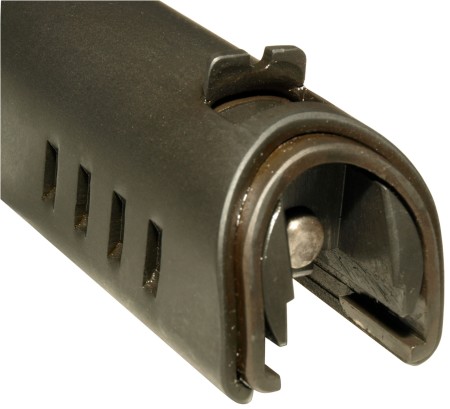
The slide housing is made of two sheet metal half-shells, riveted together at the front. At the rear end they are held together by the clenching of the finger grips into slots in the inner shell. The slide housing is then positioned around a machined bolt, only connected by two lugs on the top surface of the bolt. These lugs take all the recoil forces when shooting the Volkspistole.
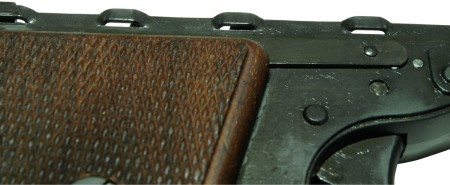
On the phosphated surface, there are only a few markings visible. The slide bears the Walther trademark (“Walther-Schleife”) on the left side and the safety is marked with the letters “S” (Sicher / safe) and “F” (Feuer / fire). Only two surviving Walther Volkspistolen are known today: Serial numbers 6 and 12. The former is mismatched with the barrel of serial number 4. The “105” is a postwar number, presumably to register the weapon. The other pistol has the number “14” stamped on it in the same way.
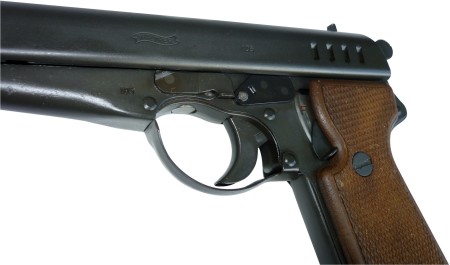
In the 70s the pistol #12 found its way back to the collection of the Walther company in Ulm, to where the former Thuringian company has moved after the war.
Special thanks to: Carl Walther GmbH Sportwaffen, Ulm/Germany
Technical data:
Length: 215 mm (8.5in)
Height: 140 mm (5.5in)
Width: 30 mm (1.2in)
Weight with empty magazine: 1088 gr. (2lb 5.4oz)
Weight without magazine: 1007 gr. (2lb 3.5oz)
Barrel length: 128 mm (5.0in)
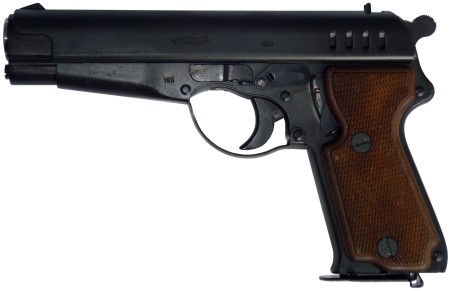
You make us jealous.
9 mm, straight blowback, stamped steal. That competes with the liberator pistols in the “things I really don’t want to pull the trigger on”.
So this is the grandfather of my SIG / Umarex Mosquito, except in place of the stamped steel components, it’s either polymer or Zinc pot metal. I think I’d rather have the stamped steel.
Thanks, Ian! Love the site!
The quality of German engineering and craftsmanship never fails to astonish. The build quality of this pistol compared to the crudity of the sheet metal 1911 prototypes is about as hugely different as you get. What an interesting profile! More aggressive than the other wartime pistol designs.
For a simplified design it still looks very finished – still requiring lots of stamping dies/tooling. First time I have seen this design – Thanks
The P-38 627 operations and app 7 1/2 man hours; any clue how many man hours this one was expected to take?
There is nothing wrong with a gun made out of stamped sheetmetal, just the same as a gun made largely out of plastic. It can be done correctly (MG-42, this pistol, etc) or incorrectly (M-60, stamped 1911 pistol).
The issue is the designer of the gun, not the material. Are they trying to “make a gun from sheetmetal” or are they trying to “make a sheetmetal gun”. I mean, do they understand the material they are using, and do they build the gun to meet it?
A good comparison would be Polymer framed pistol (like the Glock) compared to a plastic/resin AR-15 lower receiver. One was designed from the beginning to be plastic, while the other was simply made from plastic at a later point. One is a fine weapon, while the other can break if dropped or handled roughly.
This pistol looks to be very sturdy, and would fire quite a few shots before wearing out. That being said, it had a lifespan and would wear out eventually. For an owner today, this would be an issue. However, the German army in WW2 was probably less concerned with the lifespan, given the loss rate of the guns…
http://www.thetruthaboutguns.com/wp-content/uploads/2011/05/Pic-2-1024×768.jpg jk/;)
I look forward to Michael Heidler’s book! Hopefully it might include info on some of the captured weapons pressed into duty by the Volkssturm like the Italian Carcano and Danish Krag-Jørgensen and so on as well as the Panzerfäuste and the Volkssturmgewehre–although certainly these are all very interesting, as are the Sten clone 9mm 3008 SMG and so on…
Great and informative article, with good pics!
“A good comparison would be Polymer framed pistol (like the Glock) compared to a plastic/resin AR-15 lower receiver”.
You fail to realize that the plastic/resin AR-15 was designed 40+ years after the standard Ar-15. The resin technology was not even a option for Stoner when he was doing his design work. It’s called a step forward in technology.
You realize an AR-15 lower was produced by a 3D printer last week and fired 600 rounds. The testers stopped at 600 rounds because they ran out of ammo.
Dean
Dean, what’s your point?
Stoner could not use resin – that doesn’t contradict the fact that he didn’t use resin. Quite the opposite, actually.
And that printed lower needed significant redesign to work – the first attempt didn’t even last 10 shots.
Based on visual observations alone, the Volkspistole appears to be well-made ( in spite of its last-ditch role in Volkssturm history ) and definitely shows the high standards in sheet-metal stamping technology and manufacturing which the German firearms industry had achieved late in the war. Given the exigencies of that period, it is even more impressive that the weapon has a fit and finish that would still be competitive with many guns made with the advantages of peacetime resources and craftsmanship on their side. It reminds me somewhat of the beautifully precise stamped sheet-metal receiver of the StG-44 rifle.
My biggest hope is that Micheal’s book will be published in English. Then he can publish English editions of his other books too….
If I was to have any concern about the strength of this pistol, it would be the design of the guide rails. That type of feature has a habit of cracking at the base due to the metal being cut and stretched.
As for stamped metal in general, it’s very strong and light which is why it’s what all cars are made out of these days. However, the designer has to understand the process and the material, you need good stamping die designs, and you need good quality steel.
It’s a good process for mass production because with good tooling design you can run your equipment very fast. However, despite what some people say it’s not a “low tech” process. You need experienced people who know what they’re doing and good QC to make it work.
http://www.youtube.com/watch?v=tAW72Y_XPF4&feature=player_embedded
3D Printed Lower Receiver Withstands More than 650 Rounds, Gun Grabbers Panic .
Austin, Texas 3D printing innovator Defense Distributed has been making headlines the past few weeks for doing what seemed impossible at first: manufacturing quality firearms parts using 3D printers and uploading the blueprints for anybody else in the world to download, and it’s driving gun control proponents (excuse me, “gun safety lobbyists”) absolutely crazy.
In January, we reported on Defense Distributed’s groundbreaking printable 30-round AR magazine. Defense Distributed says the schematics for that magazine have already been downloaded over 200,000 times, spreading it far and wide. (Their latest revision of the magazine, the “Cuomo Series,” is available for download here).
The organization’s latest landmark gun part is a sturdy lower receiver capable of lasting more than 650 rounds, as exhibited in the group’s latest awesome video. According to the group, it has already been downloaded more than 10,000 times.
That’s a big improvement from their first attempt at a lower, which only allowed them to fire six rounds before it cracked. But this time, they didn’t stop firing on account of a material defect; Defense Distributed says their lower could easily have withstood 1,000 rounds, if they had the ammo to spare.
Ars Technica, in a detailed piece, described how the recent lower receiver improvements came about: “Last year, [the] group famously demonstrated that it could use a 3D-printed “lower” for an AR-15 semi-automatic rifle—but the gun failed after six rounds. Now, after some re-tooling, Defense Distributed has shown that it has fixed the design flaws and a gun using its lower can seemingly fire for quite a while. (The AR-15 is the civilian version of the military M16 rifle.)”
Our January report highlighted Defense Distributed’s gamechanger, a downloadable 30-round assault rifle magazine, and explained how the open-source innovation would be extremely difficult for legislators to regulate.
In a sit-down interview that was picked up by Guns.com, Alex Jones got a chance to talk with Defense Distributed frontman Cody Wilson about the success of his group’s downloadable 30-round AR magazine. “It is a symbol,” Wilson said. “They can try to go back to 94, and ban these things. But there’s new methods of manufacturing and the Internet will preserve that file forever.”
Guns.com’s David Higginbotham immediately saw the immense importance of the open-source magazine and what it meant to preserving the demonized firearm, noting, “The 3D printing that seemed like an expensive novelty (or at best a proof-of-concept) may now be an integral means of preserving the AR-15.”
Higginbotham goes on to say, “This is the start of something huge. Forgive my sense of hyperbole. I don’t think I can exaggerate this enough. The AR platform, at age 50, is going the way of the AK 47. What once was a rifle built and regulated by the postwar industrial machine, will now be built, modified, and kept alive by individuals. And there’s little the legislators can do about.”
Gun Grabbers Shaking in Their Boots
Obviously those wishing to restrict gun rights are none too happy to see these successes come to fruition. Our report from last October noted how various corporate entities tried to stifle the group’s vision early on. (See a more in-depth report in November’s issue of Infowars Magazine.)
In a segment Friday, MSNBC’s Rachel Maddow used the video of Defense Distributed’s latest successful lower receiver test to disperse fear propaganda, urging Republicans, Conservatives and the Bureau of Alcohol, Tobacco and Firearms to consider regulating the potential 3D printed weapons:
Here’s an excerpt from the Maddow piece:
These guys are doing this for political reasons. They want guns to be, not only unregulated, but unregulatable. 300,000,000 guns are not enough. More, more, more is the solution.
But whether you agree with them or not, whether you find what they are doing exciting or terrifying or both, you have to admit that this does raise all sorts of interesting questions about law enforcement, and gun laws in this country. I mean, how do you go about regulating a gun if everybody can make one themselves at home, alone, one that can shoot a thousand rounds. There’s no serial number on that lower receiver and honestly nobody bought it or sold it, it’s homemade.
How is law enforcement in this country going to grapple with homemade high powered weapons? What will they do when these guys inevitably distribute the computer code for 3D printing a fully-automatic machinegun?
At the risk of sounding like a broken pro-Second Amendment record, I’ll repeat what’s come to be a characteristic gun rights mantra: what part of “shall not be infringed” don’t you get?
The UK’s BBC also felt it necessary to weigh in on our country’s gun control debate, crafting a slick Second Amendment hit piece geared to demonize Defense Distributed and their vision………………….
Can you cite a source for this article?. I’d like to read the rest
Sorry, but that’s all there is. My source is Mr Heidler – he sent the photo and articles for me to publish.
Defense Distributed says their lower could easily have withstood 1,000 rounds, if they had the ammo to spare.
Baloney. Maybe it can and maybe it can’t but prove your theory with a test.
For something designed as a last-ditch militia weapon, this looks surprisingly not that crude.
How can they make such stuff when they are on the verge of surrendering?
thus Mr Heidler have a website he seems like a interesting person to follow
Not that I am aware of.
Hi everybody,
first of all thanks for the kind words 🙂
Unfortunately I couldn’t find any documents about this late-war pistol. Walther has nothing left today. Most was lost at the end of the war in Suhl or was later thrown away (in a time when historical documents were held in low esteem). I too think that this pistol has been reworked after its return to Walther, but again no documentation about the purchase could be found.
Oh, and yes, I have a little website: http://codebuch.jimdo.com
Nothing spectacular, just a bit of information about my books, some articles and a download-section with some wartime German manuals and documents about weapons and ammunition.
Cheers
Michael
where is the recoil spring spring located ?
is it rapt around the barrel or underneath
The recoil spring is underneath the barrel.
There are photos on the Walther forums:
http://www.waltherforums.com/forum/classics/15916-walther-blech.html
The Volkspistole example in the Walther’s possession today was refurbished by Walther Ulm facility gunsmiths after it was obtained in the 1970’s. All of these experimental pistols were much rougher and ‘in the white’ at the end of the war when they were ‘liberated’ by U.S. troops who captured the Walther Zella-Mellis facility.
Ah, that would explain the fine-looking fit and finish considering the exigencies of the time period at war’s end during which they were made. Thanks, John!
Thanks Ian and thank you Michael.
The Mauser and Walther volkspistoles are fascinating guns.
Their design philosophy is a complete contrast to the line taken by shepherd and Turpin, with their STEN, and (I argue) taken on to its furthest extreme so far by the late P M Luty, with his “Expedient” series, and “BSP” (British Standard (plumbing) Pipe Fitting), which require no lathe work, or milling.
Shepherd and Turpin appear to have envisaged dispersed manufacture in small and rudimentary shops, garages and home workshops with bench top mills, drill presses and hacksaws – inefficient and not as productive as a factory production line – but almost impossible to bomb out or close down by invasion, and their design became a favourite with clandestine builders in occupied territory.
The Mauser and Walther engineers seem to have envisaged factories with teams of tool makers to make and maintain the dies and punches necessary for the forming of those compound curves on the pistol grip and the punching to stitch together that wonderful slide. Factories equipped with power presses, rather than the fly presses and bending brakes needed for a STEN.
They also assumed supplies of accurately rolled to thickness, steel of a grade, and in a state of heat treatment and stress, suitable for the required forming operations.
Had the materials, personnel, machines, time and un bombed factory space been available, I’m sure that the volkspistoles could have been produced in huge numbers – but absolutely non of those factors were available by that time.
I’ve read that Hitler was very happy when he was first shown a captured STEN, as to him, it showed the level of desperation reached by the Brits.
If that is true, then Hitler was both correct, and very wrong at the same time:
Correct that the Brits were desperate -most of the high quality stuff had been lost on the beaches at Dunkirk.
Very wrong, to have dismissed the STEN and similar weapons, which were every bit as effective as guns requiring far better materials, and tying up more skilled personnel, and machines which could have been used far more productively on other things.
That is the true cost of anything – the alternatives you could have had instead.
Hitler once actually mentioned the Sten in a public speech, expressed his contempt and said German soldiers would never be issued such low quality weapons.
Thanks
It’s good to know that my memory isn’t playing tricks.
Taking a closer look at the pictures of the slide, it looks like the bolt/block is made from round stock, probable order of machining was to use a gang of horizontal mills to cut the clearence for the mag lips and ejector, then to use that flat to index the stock for the cut for the extractor.
It would have been interesting to see the extractor and how it is formed and attached.
and I’m guessing that the single pin which enters from the right side of the slide to retain the bolt, also retains the firing pin.
The absence of a hole on the left side of the slide suggests that once that bolt was in place, it was there to stay.
Looking at the hammer, has it been formed as an extrusion, or as a long bar milled to profile and (in either case) sliced off like slices off a sausage?
Some very good points there. The German design seems based on having the same quality and quantity of supplies and the same factory capacity as they did at their height. The volkspistole design is for quick manufacturing rather than desperation manufacturing.
Seeing the intermittent punching used to form race ways, did any of the engineers or guns find their way to Spain?
In my reading up on Spanish oddities, I found the same method used to index the bolt of the Star Z62 and Z70 carbines from rotating.
There’s a pretty good illustration of it in the exploded perspective view on page 5 of the French patent application, here:
http://worldwide.espacenet.com/publicationDetails/originalDocument?CC=FR&NR=1405239A&KC=A&FT=D&ND=3&date=19650709&DB=worldwide.espacenet.com&locale=en_EP
Although I think that having the bolt ride on rods, as in the AR18 or the M3 grease gun is a better idea than having it contact the receiver tube – which risks getting dented – I thought that the stitching looked like an excellent way to provide a track with places for dirt to get out of the way.
It’s a few years since I visited Spain, does anyone know if the “Civil Guards” (Generalissimo Franco’s Gestapo) are still using Star carbines?
Or are they now a Forgotten Weapon?
D’oh!
of course, they went to CETME, then back home to Heckler & Koch, taking the punched slideways and applying them to the slide of the H&K P9
Keith’s comments about guns designed to be quickly and effectively manufactured in dispersed small workshops without the need for specialized machine tools ( see his post on Mar. 7, 2013 / 1159 hrs. ) reminded me of yet two more forgotten weapons — the British Hefah V Mark I in 0.303″ Enfield caliber and the BSA gas-operated LMG, or Besal, also in 0.303″.
The former was developed by the Ductile Steel Company of Short Heath, and was submitted for testing in June 1940 as a possible infantry LMG to supplement the Bren ; it used a modified Lewis action with a conventional return spring in place of the Lewis’ clock-spring and rack, a single-lug bolt and bottom-mounted drum magazine to simplify production. The Director Of Naval Ordnance, desperate to alleviate the chronic shortage of AAMG’s for small coastal patrol craft, recommended it’s adoption and the Hefah Company of Wednesfield was founded to manufacture the gun for the Royal Navy. After a relatively small production run, the gun was declared obsolete in November 1944, the once-feared shortfall of Bren LMG’s having long since been resolved through increased production and the Luftwaffe’s failure to adequately target the Enfield production complex ( where the Bren was made ).
The Besal was designed by one Mr. Faulkner to take advantage of the production capabilities of small dispersed machine shops in the event that the Enfield works making the Bren should be seriously damaged. It used the same magazine as the Bren, and was composed mostly of commercial-grade steel tubing and stampings, there being few machined or forged components. To further simplify production, the gas piston and breechblock were actually of square section, the block being locked by two lugs that engaged corresponding recesses cut into the receiver. The Besal was cocked in similar fashion to the BESA MG, i.e., by pulling the pistol grip rearwards. In spite of its obvious and somewhat drastic simplification in the interests of quick and easy manufacturing, the gun still featured an adjustable four-position gas port and a quick-change barrel with fixed handle. The bipod was of fixed height, and a basic two-position rear sight was fitted. By all accounts, the Besal was a very impressive gun in spite of — or perhaps because of — its simplicity. It proved to be reliable and accurate during acceptance trials, and was formally approved for production. A small pilot batch of guns was made, complete with production drawings and schedules, after which the whole package was put on the shelf as a hedge against an emergency. This, of course, never happened , and Bren production continued basically uninterrupted throughout the war to meet the needs of British and Commonwealth forces.
I don’t know if any fully-intact working examples of either gun still exist, but I imagine it would be both amazing and very educational if someone were to present a demonstration of one or the other.
Both the Hefah and Besal will be on the site sooner of later – I have a manual for the Hefah and photos of a Besal. I wasn’t able to shoot it, but I did take it apart and get detailed pictures. 🙂
Ian, I think I’m not the only one having to wipe the saliva off his chin :). Thanks for the heads-up — I’m definitely looking forward to this!
Earl, thanks for the reminder and info on the BESAL and HEFAH.
I’m looking forward to seeing Ian’s take on them.
Interesting; Polish wikipedia has better coverage of the Besal than the English language one.
much of the piece looks like it was lifted from the archivingindustry.com link in the references
http://translate.google.co.uk/translate?sl=auto&tl=en&js=n&prev=_t&hl=en&ie=UTF-8&eotf=1&u=http%3A%2F%2Fpl.wikipedia.org%2Fwiki%2FKarabin_maszynowy_Besal&act=url
That has quite the sleek look for a last resort weapon.
It would be very cool to have a side by side comparison of this and the Finnish VKT/44 pistol, a broadly similar design. (pics of the vkt pistol here: http://imgur.com/a/d3W7S )
Seeing how rare they both are, that is sadly not likely to happen.
Very informative post indeed. Thanks for Ian and commenters.
Close up photo of muzzle end of Volkspistole shows, as if, rifling is made rather
deeper to exhaust some gasses to lower the chamber pressure during firing for
secure using of 9mm Para. bullet with simple blowback operation which same concept
was used in the forerunner of plastic pistols, VP70 afterwards which was also a
member of volkspistole category.
I have actually fired one of these Walther pressed steel pistols that a friend has. The recoil was supriseingly light and nowhere as bad as the Liberator or the current .410 revolver. I started to think why the Germans bothered to manufacture the P38 when they could have had so many more of these. The accuracy was good as well
Timing. When the P38 was designed in the mid-thirties, it was a lot easier to manufacture than the P08. A big step forward for the people at the time. On the other hand, steel pressings in small arms manufacture were still considered a kind of heresy by many. Nobody in the small arms industry had the necessary expensive equipment. Only very few people in the mid-thirties actively promoted steel pressings.
Apart from that, its not so much the decision to go for pressings, but to build-up the know-how to make it work that takes a lot of time.
The whole area of steel production in the world wars could make a very interesting study.
I think the SAE were well ahead of the British central planners (always the case with anything that is actually worth doing) in producing a format for standardizing steel specs.
The British bureaucrats came up with a system called “emergency numbers” or EN.
perhaps for reasons of “security” (always a convenient post hoc)or more likely for reasons of bureaucratic ignorance, the EN numbers bore no discernible relationship to the composition of the steel – you needed a copy of the spec sheet to interpret.
The obvious ones which stand out in my memory are;
EN1 engineering grade mild steel
EN1a free cutting mild steel (leaded or sulphurized)
EN8 0.4% carbon (SAE 1040)
EN19 (covers both SAE 4140 and SAE 4340)
all well and good, however, even now, our analytical techniques leave room for nasty surprises – like Beretta slides snapping in half (it is designed with stress raising square cornered cut outs in its thinnest and most highly stressed place, so it is ideal for showing up sub standard steel) due to trace elements in the steel used.
Take that back to the late 1930s and early 1940s with wet chemistry and (perhaps) film based arc spectrometry as the best analytical techniques available, both were expensive and slow.
Prior to the war, a commercial user of steel would buy a known maker’s named steel.
The steel was made from a known source of raw materials (different ore deposits can contain markedly different quantities of trace elements, such as nickel, phosphorous, vanadium, titanium etc), in a single plant – so any trace elements were pretty consistent between batches, as were the process factors, like the de-oxidizing (“killing”) procedure, how long the steel was allowed to stand in the ladle for the debris from de-oxidizing to seperate, what the dimensions and proportions of the ingot mould were, and hence how much fractional crystallization and compositional segregation (“rimming”) could occur during solidification, and how much of the top of the ingot was trimmed off and how deeply it was de-barked before rolling.
Even in the rolling or forming process, factors like the temperature at which rolling was stopped re-heating was undertaken, and the ammount of working in each pass through the rolls affected the grain size and grain orientation and the state of locked in stresses in the steel.
As a result of trial and error, each user found steels which worked for them, and they stuck with that maker. It generally worked.
So far, I’ve only stumbled upon fragments of the ensuing centrally planned chaos.
The most frightening of those was the habit of Liberty Ships to begin snapping in half as soon as the temperatures went below about 5 degrees Celsius (about 42 F).
This was even happening in port, so it could not be dismissed as torpedo or mine damage. Heaven only knows how many were lost due to embrittlement in the North Atlantic, one figure which a gargle search spits out is 140 liberty ships lost a month due to structural failure.
The problem was initially thought to be due to their welded rather than riveted construction, not allowing any “give” in the joints between the plates.
That was actually partially true, and there were also problems with hydrogen embrittlement and compositional changes due to trace elements preferentially going into the weld, both of which were cured by reheating to stress relieve the welds.
The main problem was the steel being used, its impact strength suddenly dropped as it went through a brittle transition at about 5 Celsius. I forget the exact compositional cause and the cures which were found (iirc part of the cure was increased manganese, which both aids deoxidation and lessens the embrittling effects of sulphur and phosphorus)
The metallurgy-related issues that you brought up in the example of the Liberty ships is a very good illustration of how critical it is to have the correct type of material for a given application, firearms included. I remember reading up on the subject ( of structural hull integrity concerning the Liberty ships ) many years ago. Basically, the less ductile steel used in earlier hulls experienced the issue of excessive brittleness at lower temperatures due to the annealing effect of the welding process that hardened but stiffened the steel in the heat-affected zones of the weldments to the point that the combination of existing load stresses and sea conditions put those zones close to the point of structural failure. The added temperature factor was probably just enough to push those hulls over the edge.
Do you have any additional information from Kaiser Shipbuilding ( the original designer and builder of the Liberty ship design ) concerning this topic?
Hi Earl,
Unfortunately no, I don’t have direct info, I only know of the problem as one of the most drastic examples of a materials mess up.
The Liberty Ships problem also seems to have brought the problem of relatively high temperature ductile to brittle transformations in steels, to a more general audience (including to me).
Interestingly (or worryingly!) according to my old (xerox)copy of Lula http://www.amazon.co.uk/Stainless-Steel-R-A-Lula/dp/0871702088 martensitic (4 series – the heat treatable stuff generally used in guns) stainless can undergo a ductile to brittle transition at around room temperature. I have read about brittle failures of stainless barrels during extremely frosty weather in places like Finland and Alaska.
The wider point I was hoping to think through for myself and to make (I got badly side tracked along the way) was the largely hidden complexity of selecting a suitable steel for a particular purpose
and
that the complexity of the problem was even greater with the slow and limited analytical chemistry and physical testing techniques available in the 1930s and 40s. Chances are that no one actually knew why steel from a certain source would do certain things but the same spec steel from a different source wouldn’t.
and
That the steel could not be simply ordered from the chosen source and paid for
– everything was subject to the central planning chaos of both national socialism, and war socialism –
those complications of steel selection almost certainly went over the heads of the various politically appointed central planning nomenklatura (whether they were in Germany, Britain, the United state or the Soviet union). The temptation to issue orders saying; “you, steel maker, make x tons of this specification for these users” must have been overwhelming.
Michael Heidler’s inclusion of the exchange of memos with the central planners about priority, gives some indication of the chaos involved. The decisions of what was to be made, in what quantity and by whom, and who was to get the product – all fell to the whim of some political appointee.
Hi, Keith :
Thanks so much for the informative reply. I guess the topic concerning the Kaiser-built Liberty ships will require more extensive materials research and evaluation over time. That was an interesting observation about martensitic stainless steel usage in firearms and the related brittleness / temperature sensitivities under what are probably very particular and unique circumstances. Alternative grades of stainless steel ( such as austenitic and super-austenitic stainless ) may have certain more desirable physical properties, such as the ability to satisfactorily accommodate a much wider range of operating temperatures while still retaining an unchanged molecular structure without distress, but this is unfortunately negated by other firearms-specific metallurgical factors such as reduced resistance to galling in very tight mechanical tolerances over repeated high-stress cycles, and extreme pressure impulse cycles without distortion ( such as the extremely high momentary chamber pressures that occur when a cartridge is ignited followed immediately by a huge pressure drop as the bullet leaves the muzzle ). Perhaps the answer to getting the best of both worlds lies in the realm of duplex and super-duplex stainless steel as well as more complex derivative stainless alloys, but whether or not firearms manufacturers deem it cost-effective enough to warrant time and resources is another matter.
If Germans industry strongly decided to made weapons like simplified Volkspistole in, say 1940. or 1941. instead of the late 1944. course of the war on the eastern front could probably be very different… They opted for high quality guns and weapons that they at one point started to lose at much higher rate than they could replace them (along with the people), a fact that the soviets were not having a huge problem, with their simple, cheap and rugged weapons. The paradox of their “superior” thinking is in spending the last resources on the handgun, item that is cool to have, but that has absulutely miniscule effort on the battlefield. The allies reorganized their industries for mass war production in 1941. and the germans started to think about it only after the disastrous events in 1943.; this is very valuable lesson from the history. Japan is even more tragic story, and their initial success is a miracle compared to their relatively weak industry output. But, looking at them today, seems like their learned their lesson in the economics, as they opted for economic, instead of military superpower approach !
(Not related to article, but the comment section)
Wow this has got to be one of the most in-depth and informative, well-intentioned (non-inflammatory) comment sections I’ve seen recently. If only most others were like this one.
This has got me all hot’n’bothered about metallurgy now, time to go take a wikipedia bath… with a ducky of course.
How to make $10,000 Per day FAST: http://gmy.su/:TWuQ?o0l8kN