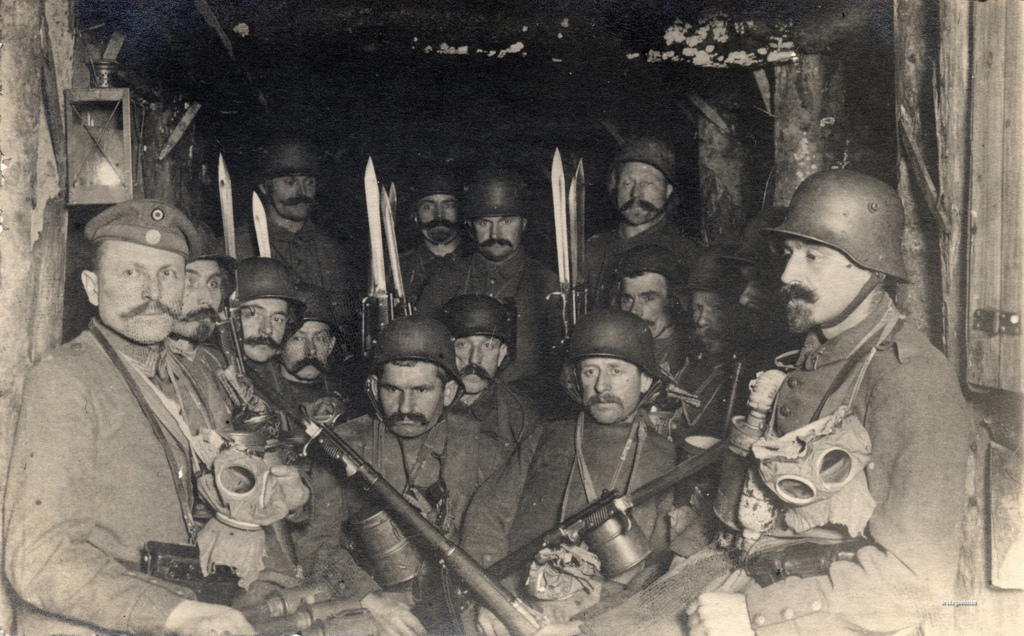
Interestingly, one of the German troops in the front row is wearing grabenpanzer steel armor. This was reportedly used primarily for machine gun crews and sharpshooters – soldiers whose jobs were particularly heavy on staying in one place and being the target of lots of fire.
Incidentally, does anyone have a good knowledge of the metallurgy of this armor? I am getting a reproduction set from IMA to do ballistic testing on, and I would like get some idea for how close it is to the originals in functional terms. Any documented information on composition, hardness, etc would be much appreciated!
I believe they used a nickle steel mix.
Maybe i have some info about it.
Havent the execelent Deutdchn Waffenjournal made an issue of this very intresting subject?
I’m sure that both the French and British authorities at time handed this issue to the Steel laboratories at time, the American compy might be easier to find.
Good luck!
Fascinating topic! The linked product under descriptions says originals were brinell hardness 360-520 and it was silicon nickel steel capable of resisting rifle bullets at 60 yards. It also mentions that the reproduction isn’t at original spec.
Another fascinating thing on that link is image 12 of 12 which shows 4 soldiers in this armour with some fascinating looking weapons. The first looks like an automatic rifle/light machine gun. I’d actually say a captured 3006 chauchat if I didn’t know better? The guy on the right seems to have an anti tank rifle of some sort. Those more knowledgeable than me might be able to identify the weapons?!
Going from left to right, No. 1 and 2 are holding Chauchats, specifically the American .30 caliber version with the ‘straight’ magazine rather than the crescent-shaped 8mm Lebel version. The “mill file handle” foregrip sticking straight down is a dead giveaway.
No. 3 has a K98b Mauser, 7.9 x 57, standard “short” rifle, introduced in late 1917 because the “Lange” Gew98 was just too unwieldy in a trench raid. it would soldier on as the standard Wehrmacht infantry rifle well into the early WW2 period when production of the Kar98K finally caught up to demand, and was still used by reserve and allied formations in ’45.
No. 4 is holding a Mauser “Tank-Gewehr” anti-tank rifle, 13 x 99mm single-shot. That alone puts this shot no earlier than the summer of 1918 because those didn’t start reaching even special troop nits until about mid-May.
It would definitely hole the armor on the British Mk I “rhomboidal” tanks, but the later MK IVs had face-hardened armor to defeat such rounds after Hotchkiss and Vickers developed their 11 x 59mm rounds for “anti-balloon” AA MGs, which Vickers also developed with an AP bullet for shooting at armored “aeroplanes” like the Hannover.
The 13mm’s main claim to fame is that according to Chinn (The Machine Gun, vol. 1), the early U.S. program to develop a 0.50in heavy MG was built around a .50 round with about the ballistics of the French/British 11mm (MV about 1500-1600 F/S with 350-400 grain bullets). Later developments got that up to 2,400.
Then captured “T-Gews” and their ammo arrived at Aberdeen, and in tests showed MVs above 2,700 F/S, with a heavier (800-grain) bullet, at that.
Pershing immediately ordered Ordnance (and John M. Browning at Colt) to go back to the drawing board and come up with a “fifty” round and gun that had the ballistics of the German 13mm AT rifle.
We’re still using the result of that project today. We call it the Browning M2 HB 12.7 x 99mm aka “Fifty”.
cheers
eon
Tanks aye, they were 1917 etc.
That photo might be Camembert then, Cambrai…
Our bit of mobility.
3rd from left has a Kar98a. Kar98b is the same length as the G98, and is post-war.
Oh, wait, it might not be. Looking at it on zoom, the last-band-to-muzzle distance looks too long, the sling looks like it’s mounted on the bottom, and the rearsight looks pretty bulky. Also, it’s longer than the CRSG’s. I suspect actually it’s a plain vanilla Gew98.
One thing it can’t be though is a Kar98b (introduced 1923).
Wonderfully informative eon. Fascinating about the origin of .50 BMG! The picture possibly suggests there wasn’t a reluctance to field captured weapons if the Chauchats are more than props for a photo. That US version was pretty notorious for it’s reliability issues in the .30-06 chambering so it raises a few interesting questions.
1.I think that, especially Storm Troopers, would not have anything German-produced at the time which would effectively combine maneuvrability with a sustained fire support in the trench raids.
2. That remark is off-tangent: unless facial hair was a mark of some sort of corps d’elite (like the engineers of the French Foreign Legion), would the introduction of gas-masks militate the elimination of the superfluous hair (not to mention the lice)?
Regards, Andrzej
“were brinell hardness 360-520 and it was silicon nickel steel capable of resisting rifle bullets at 60 yards”
So far I know:
-original WW1 German sniper’s shields were 8mm thick, some British soldiers get .600 Nitro Express rifle which were able to penetrate it, so Germans start to use two shields together for summary thick of 16mm
-Austin Armoured Car were initially armed with 3.5-4mm, but it proved be too thin, so it were uparmoured to 7mm.
-early field attempt to get armour-piercing capability from rifles was reversing bullets
Even sillier than this issue of Nitro-express stuff is the Fascist Italian attempt to get machine gunners behind mechanized cover, the Motomitragliatrice blindata d’assalto, which was essentially a one-man tankette with no real purpose apart from protecting the gunner as he made a slow, uncomfortably crouched advance towards the enemy lines (there is no floor plate, and I doubt the controls would give you any speed above 5 km/h). I suppose a French Lebel-Grasset or Daudeteau-Rival would have made mincemeat of that joke of a tankette. And even the crappy Japanese Type 94 tankette would be better than a one-man motorized machine gun (or 45mm Brixia mortar, which was another weapon that could be mounted in the laughable vehicle).
I suppose the real reason would be providing inexpensive and not complex way for the countries making their first forays into the armor.
Regards, Andrzej
Typical today’s APCs armour is 8mm (5/16″) thick and is at around 240BH hard. It is supposed to stop 7.62 NATO fired at point blank (not AP type).
Are you sure with that BH? In my recollection anything above 200 is pretty good already. Hardness of 220-250 and up is really tough/ hard – assuming mid to high carbon steel.
I’ve got to revise that… http://www.steelexpress.co.uk/steel-hardness-conversion.html
What you are saying may be possible.
Silicon-nickel steel according to Modern Body Armor by Martin J. Brayley
I think that’s a trench storming team… Their attempt, to get some mobiiity into the war. Which they thought they did, but the “war was lost, around them boo hoo cue Adolf” shock troops, they all look mad as carrots. Mind you, you probably would. I wouldn’t be at all surprised if everyone on this photo all got mown down, riddled with bullets, smacked with a spade and generally mauled like hundreds of thousands of others. Merry Christmas, that armour would be circumvented by sticking both your fingers in their eyes when they slithered in front of you from the muddy parapet.
It’s 1916 onwards, no spikey pickles.
Mobility achieved via, the enemy trenches weren’t particularly far away in some circumstances, they figured the armour would give a few chances to throw a grenade etc in the trench take out a few defenders before they got it, which undoubtedly they would, but it was stalemate seconds count, throw, bang! Thud. Instead of just thud.
Feck that right off, hundred years ago, it can stay there.
_Helmets and Body Armor in Modern Warfare_ by Bashford Dean 1920, Yale University Press.
Prof. Dean describes German body armor at some length:
“This body armor is made of a silicon-nickel steel, of which the formula is as follows:”
(He goes on to describe percentages from three different sources)
Carbon… .38 .20 .39
Chromium .22 .21
Copper… .17
Manganese .60 .98 .58
Nickel…1.55 4.12 1.55
Phosphorus .022 …
Bashford Dean also briefly describes ballistic tests against American rifle ammunition, quotes captured documents and provides a few detailed drawings in a section dedicated to German armor.
Thank you! Yes. This!
The book is downloadable as a PDF file from the Internet Archive. An excellent resource on WWI steel helmets and various styles and types of body armor.
Glad to be of help. I had forgotten that Bashford Dean’s book is available as a PDF online. I got my copy the old-fashioned (1980s) way: Interlibrary loan and a lot of photo-copying.
I like how they all have the same mustache.
SPECIAL BONUS!!:
Ian has photoshopped himself into this photograph! Can you find Ian?
The “Grabenpanzer” armors were made by Krupp, as indicated by their three circle logo which is visible on existing armors. So maybe they can tell more about the type of steel, although I fear they are hesitant to dig in these darker parts of Krupp’s history. But it is a start, and old German book about metallurgy might help further.
Look at the conditions of their gas masks! Wouldn’t answer a fire call as a Volunteer wearing something that shabby today.
I saw a tv documentary about synthetic club drugs and the host went to a chemical plant in china that manufactured chemicals used in synthetic marijuana on an industrial scale for export. The Chinese chemist that were making the stuff were wearing gas mask that looked identical to the ones these soldiers are wearing. Got to love those Chinese labor laws.
The steel plate armor will protect you against most blades and bullets but will not withstand tanks, artillery, or giant rocks… No wonder body armor wasn’t really a thing until synthetic fibers came along. I don’t know if B-17 and B-24 bomber crews’ flak jackets would stand up to real flak. Historical trend is that the guns usually beat armor, be the armor on one’s person, on a wheeled or tracked vehicle, or on a ship.
Which of these would be best for taking on armored mobs?
1. Type 97 AT Rifle
2. MG 18 TuF
3. 8.8 cm Flak 36
4. M61 Vulcan
5. Conveniently placed giant rocks on a hill…
6. 32 cm railway gun
7. Add your favorite toys to this list!
This questionnaire is not a mandatory item. Ignore it if you wish.
Well if God really was with you, you could have him tear asunder Biblical sized rocks of like verily epic proportions and simply drop them on your enemies.
Battle group 6 etc Verdun, pray, pray, pray, Mt Everest, weeeee, splat. Beat that.
That’s only if God were to answer your prayers as you think he’d answer them. More likely, if the Almighty were on your side something more subtle (though just as significant) would happen. Although there was that instance of an instant hail storm somewhere in the Old Testament and a whole ton of plagues…
They lord works in mysterious ways, dystentry or something a plague of… Wasps etc, amen.
Kneecap placed .22s will do. Sniping is always firepower by hits.
“7. Add your favorite toys to this list!”
14.5mm Slostin machine gun
Initially, USAAF bomber crews wore British “flyer’s armor”, the “Type A” full vest, “Type B” half-vest, “Type C” sporran (short apron), and “Type D” full apron. These were “soft” armor units made rather like a brigandine, of canvas containing overlapped 2″ square plates of 1mm Hadfield manganese steel. The full “A” vest, armored front and back, weighed 16 pounds, the “B” which was only armored in front, weighed 7 lbs. “A” was generally only worn by gunners, who were mostly standing up; seated crewmen and ball-turret gunners wore the “B” vest because their seat backs were supposed to be armored.
Trivia note; All these vests were made by the Wilkinson Sword Company.
The U.S. made and designed vests that succeeded them were developed by the Armor Workshop of the New York Metropolitan Museum of Art (MOMA) under contract to U.S. Army Ordnance. (They had more experts on steel body armor than anyone else on Earth at the time.) Their first product, the M1 vest, was more-or-less a duplicate of the Wilkinson “A” vest, even to the same Hadfield manganese steel (which was also used in the standard U.S. GI M1 “pot” helmet).
This was followed by the M2 vest, which was similar to the Wilkinson “B” vest. Both could use either the M3 (sporran, “C” type) or M4 (wide, “D” type) armor aprons. There was also the M5 groin armor, which was put together the same way but covered the upper legs like a lap robe; it was intended for seated flyers in armored seats.
In late 1944, two similar vests, the M6 and M7, were developed, that allowed for backpack parachutes to be worn (as opposed to seat-type ‘chutes). These were issued mainly to B-29 crews in the Pacific.
More developed “hard” vests, the T1 through T6 series, using shaped sections of Hadfield steel similar to 15th Century “plate” cuirass armor, were developed in 1944-45, but none ever actually saw combat service.
Neck protection was by the T59 series neck guards, which were front and back halves made of stamped Hadfield steel, and covered with canvas on both sides with a fur lining on the inside to prevent chafing or frost injury at high altitude. Head protection was by the modified M1 helmet initially, with the sides spread by a screwjack and then cutouts made for earphones. This was replaced in 1944 by the M3, a modified M1 with larger hinged steel “cups” over the earphones and a separate liner.
There was also the M4 or “Grow” helmet, which was a soft leather helmet rather like an (American rules) football player’s helmet of the era, with five stamped “arches” of Hadfield manganese steel inside it, worn over a standard soft leather or canvas flyer’s helmet. This was intended mainly for fighter pilots and “back seaters” (P-51, P-61, etc.) who couldn’t wear a steel helmet under a canopy.
Postwar statistical analysis showed that while helmets did not change the number of KIAs due to head hits materially (35% without, 36% with), they reduced wound percentages from 65% to 21%, with 43% of those hit in the head suffering no injury. Body (torso) armor reduced KIAs by more than half, from 37% to 15%, and WIAs from 63% to an impressive 12%, with 73% escaping any injury. Groin/lap armor was even more effective, cutting KIAs from 33% to 7% and WIAs from 66% to 11%, with 82% escaping any injury other than maybe a bad fright.
Altogether, armor overall cut KIAs exactly in half, from 36% to 18%, and reduced WIAs by a genuinely amazing factor of 69% to only 13%, with 69% of airmen wearing armor not being injured by hits.
Armor was clearly a handy thing to put on before flying over “Festung Europa” and Japan.
Source; Sweeting, C.G. Combat Flying Equipment; U.S. Army Aviators’ Personal Equipment, 1917-1945. Smithsonian Institution, 1989. Chapter IV, “Armor for Aviators”.
Record of Army Ordnance Research and Development, Helmets and Body Armor. Office of the Chief of Ordnance, Washington, D.C., January 1946. Vol. 2, Book 1, Section 3.
cheers
eon
The flak jackets worn by B-17 and B-24 ( and other American bomber ) crews were typically made up of overlapping manganese steel plates sewn into the jacket casing. They were intended mainly to provide protection against low-velocity projectiles such as flak fragments that had already expended most of their energy penetrating into the interior of the aircraft, but which could still cause serious injury or death to unprotected aircrew. They were not designed to prevent penetration by direct hits from high-velocity projectiles.
The New York Metropolitan Museum was involved with body armor research during WW1, and after the war ended they released a book called “Helmets and Body Armor in Modern Warfare”. You can read it online here:
http://www.archive.org/stream/helmetsbodyarmor00deanuoft#page/n0/mode/2up
The German body armor in the picture has a detailed rundown on pages 142-147, including the composition of the metal, field reports, ballistic tests, and physical analysis.
Aha, great! Thanks very much for the link!
testing historical plate armor is always a bit tricky , the surviving pieces are usually very expensive and the historical data that is available usually isn’t good enough to make good replicas
The Metropolitan Museum of Art made a good video showing actual medieval armor being used https://www.youtube.com/watch?v=NjKbi7YUNaI
if the armor was used primarily used by machine gun crews and sharpshooters i would think that the armor would be worn on your back and not your front
i am assuming that your belly would be pointed to the ground or the inside of a trench if you are a sniper or manning a machine gun
and your back would be pointed to the sky most of the time and that’s where the shrapnel comes from
also how encumbering is it to where (yes i want to see you suffer (for science of course))
the armor covers a part of the shoulders would this hinder a sniper
juver, while I’m inclined to agree with your points about armour not protecting areas of prone soldiers like the back from shrapnel or shell splinters but I think they were imagining soldiers standing in trenches or seated in them looking over parapets who needed protection from bullets while pushing back assaults and holding positions. Might have been useful too (in theory at least) for following a creeping barrage during an assault where your own shells or grenades fragments might be a hazard.
You sit behind an MG08, which is why it’s frontal armour.
Whenever I see soldiers from the Great War, and they all have bayonets, why aren’t they wearing chain mail? One makes as much sense as the other.
Mail would be too easily circumvented by switching from knife or sword bayonets to the use of a spike-type bayonet.
Chain mail was rendered useless by the long bow and the war hammer during the Middle Ages. Anyone with a nice sledgehammer or an axe would easily dispatch mail-clad shock troops. And officers of the Imperial Japanese Army would just try to decapitate the chain-mailed individuals with their swords after pinning them down.
Fascinating photo, I love shots like these.
Looking at it, the first question I asked myself was did Ian photoshop himself into the picture as German soldier on the right.
That is one hell of a photo collection!
The postcards are kind of hard to read, but worth it.
They are facing slaughter and their expression says that. Some of them will be soon gone.
As far as moustache or goatie facial hair, this was apparently common with other troops such as Russian and Austro-Hungarian too. One unpleasant affair with this aesthetic edition is the fact that gas mask may not fit snugly enough and if it does, it will cause inside intense sweating. No good.
I recall what it means to wear gas-mask and conducting “speedy relocation” with usual combat pack on the back; nothing especially pleasant – even without moustache.
Hi, Denny — great to hear from you again and to read your highly-informative comments. Hope all is well with you and yours.
I agree with your assessment of carrying out high-stress battle drills ( or being engaged in combat for that matter ) while having to wear restrictive PPE such as this, with all the breathing resistance and ventilation restrictions it imposes. Those of us who also had to undertake such tasks while dressed in NBC gear will remember all too well what the process entails.
Likewise, Earl!
You had been my “humanitarian concerns” companion in past and I appreciate it. We all know (but rarely admit) that to fight well and with dedication one needs among other things, to be a full-value human, as contradictory as it may sound. There must be a solid cause.
I am doing relatively fine, although age is knocking on my door; my general health is not bad with some small indications showing up. I have hope in my children to carry on with the gene:-))))
True, breathing under rubber is not fun and you are certainly familiar with that art.
IMA writes:
The original silicon-nickel steel armor (don’t try this at home) was generally proof against rifle caliber gun bullets starting from about 60 yards and provided protection from the concussion of grenades and artillery shells and also light shrapnel. The hardness of the metal on the original armor (not the reproduction!) was Brinell 360-520 which was much, much harder than mild steel
My opinion is to ask a steel company like Nucor Corporation or United States Steel Corporation if they have the steel.
Otherwise you can get a WW1 German helmet and do a metallurgy test on it. Either way I wonder if thoee companies would sponsor the video or use your work in one of their commercials.
Honorable Mr. Cherndog:
Please add one of my favorite toys to the list: KraussMaffei Wegmann Rheinmetall Landsysteme Puma with fully stabilized, automatic 30 mm MK30-2 ABM with a 200 rounds per minute rate of fire and an Effective range up to 3000 m. If that does not suffice, you can always run them over with it.
That is one way to end the argument: VEHICULAR HOMICIDE! I think the British did the same during the Korean War with their Centurion tanks. So much for mob attacking the tanks… In that case, I guess the Tiger I or a company of Semovente 90/53’s (or even some flamethrower versions of the L3/35 tankette to counter anyone who gets too personal) would be a good complement to go with the Puma just in case the mobs brought in some bigger mechanical friends.
And almost 60% of modern steel making is done by the Basic oxygen steel making resulting in a purer tougher steel than steel done in WW1.
You probably meant the Bessemer oxidation process in which most of undesired carbon, phosphorus and sulphur contained in raw iron is removed. http://en.wikipedia.org/wiki/Bessemer_process
Some amount of carbon has to be retained (typically at around 2%) to maintain resulting product’s – steel its strength. Pure iron per see is soft. Hence word “purity” may be easily mis-interpreted.
I believe there are two separate directions of discussion here. One it the mentioned basic carbon steel a the other are highly specialized alloys such as steel with purposely controlled contents of nickel and silicon (i.e. “Krupp steel”). The body armour of pre-Kevlar era may have been good application for this material.
No, I meant basic oxygen steelmaking.
http://en.wikipedia.org/wiki/Basic_oxygen_steelmaking
German WW I body armor was a carburized nickel-chromium steel alloy known in the USA as “E3310 Krupp Modified”. Carburizing practice was effective case depth 15 – 25 percent of total thickness. Surface hardness was 60 HRC pluss, core 38 HRC minimum.
Today,AISI/SAE E9310H is used in applications where “Krupp Steel” used to be used. Lower alloy content, but superior properties after carburizing. AISI Type P6 tool steel is closest current steel to “Krupp Steel” chemically. Neither modern grade is readily available in sheet or plate product forms.
“AR 500”, a low alloy through hardened plate whose composition varies by thickness, is the current grade of choice for homogeneous armor sheet and plate. Its ballistic performance is quite comparable to “Krupp Steel” at thicknesses under 12.5mm.
Very interesting stuff about the variations of the steels available and used!
I think what Ian was asking about regarding “… how close it is to the originals in functional terms. ” is probably about mobility – weight, flexibility, etc. I suspect he’s going to put some on an try shooting at stuff (but not at something that shoots back!)
Hi everyone, as luck would have it I’ve actually come across a book which seems to cover this topic pretty extensively
The book is well worth a read as it covers the development and use of helmets, body armour and bulletproof shields by all the countries involved in ww1.
The book is called
Helmets and body armour in modern warfare, Dean Bashford (Yale University Press, New Haven, 1920)
I downloaded it as a pdf. from the site linked below
https://archive.org/details/helmetsbodyarmor00deanuoft
The information that you’re looking for regarding that particular type of German armour can be found from page 142 down
Just in case anyone can’t access the book I thought I should copy out the passages relating to the armour’s chemical and physical characteristics and post them here. My understanding of metallurgy is very limited so I can’t offer any commentary on it, but hopefully this information will be interesting to anyone more knowledgeable and useful for comparing with the modern reproduction
the copied passages are below
1. chemical composistion
I*
Carbon .38
Chromium .22
Copper .17
Manganese .60
Nickel 1.55
Phosphorous .0222
Silicon 1.75
Sulphur .006
II†
Carbon .20
Chromium –
Copper –
Manganese .98
Nickel 4.12
Phosphorous .013
Silicon 2.135
Sulphur .073
III‡
Carbon .39
Chromium .21
Copper –
Manganese .58
Nickel 1.55
Phosphorous .20
Silicon 1.95
Sulphur .01
*analysis of an abdominal plate (model 1917) made by universal rolling mills
†analysis made by order of British general headquarters in France model 1916
‡analysis received (February 1, 1918) from H.A.E.F.: the composition of the main plate is here given
2. Physical characters
Unaltered by annealing and capable of being drilled. Tensile strength (square inch) 65.69; elongation 1 percent; hardness, Brinel test 360-520
3. Ballistic tests
American rifle ammunition at 2,140 foot seconds pierces at 30 yards but is resisted at 60 yards
Service ammunition of full velocity (2,780 foot seconds) shatters at 60 yards is resisted at 300 yards
In cases of failure lamination of metal was noticed
Also according to the book this armour came in two sizes one larger than the other. The smaller version weighed 19-22 pounds and had an average thickness of .140 inch while the larger version weighed about 24 pounds and had an average thickness of .131 inch.
source: Helmets and body armour in modern warfare, Dean Bashford (Yale University Press, New Haven, 1920) pp.143-144
That book’s a great find, Kernowboy.
Interesting…. with this Carbon contents being so low it cannot be successfully hardened (0.8% is considered as minimum), but its hardness is on par with “pre-heat treated” steels of today say grade 4130-4140. Machining using high-speed steel tool bits is still possible with this hardness.
Regarding the hardening of low carbon steel, could they have been case hardened or carbonized? That would account for hardness even if they were annealed.
Yes, low carbon steel can be cased (enriched with carbon to given depth) and then hardened. That would however in this case, deny purpose of alloying elements. So it is one or the other, not both. But, this is just my take based on my experience, I may be wrong.
When comes to annealing previously cased and hardened part, I do not see sense in it, IF it is even feasible. However, case hardening is used widely on gun parts and that is primarily for wear endurance. The case thickness is relatively small, typically just 0.010-0.015″ with parent material normalized beforehand.
Denny,
The (US) Army report said that upon annealing a sample the hardness of it was not altered (as they were examining it) . The idea being it was not heat treated to increase hardness, hence the possiblity that it had been case hardened instead.
It seems to me that both the centre-front soldiers are wearing grabenpanzer body-shields.
Does “ballistic testing” meaning “shooting full of holes”? I’m not sure I would see the point of ruining a mild steel repro in this way.
Otherwise, I would very much like to see Ian running a pistol carbine course wearing a stalheim with brow plate, grabenpanzer, greatcoat, jackboots and, say, a long Luger with holster-stock and snail drum.
In my experience almost any low-carbon steel (or iron for that matter) can be “case hardened” to some degree. I have often used various methods ranging from the old “rawhide wrap” method to the use of converted electrical heated ceramic sintering ovens and some microwave ovens. Even Titanium can be “case hardened” for some uses. One of my hobbies is building high-pressure (in excess of 2,500 psi) and Pulse-Detonation rocket engines. My specialty is in Titanium machining and treating. One example is making Titanium nozzles and “case hardening” them as above. Where a Graphite nozzle will take only one burn and an Inconel will withstand maybe five, the Ti nozzle will usually withstand 15-25 under the exact same conditions. It also emerges from the process with a jet-black lustrous finish that appears to be almost translucent or has “depth” as painters term it. The only thing I have found that will surpass them is melted and poured Aluminum Oxide (plus additives) Cast Ceramic. But this takes a high-powered microwave over and an Argon atmosphere as does the Titanium nozzles. On all the above, the only thing I have found that will scratch them is a natural diamond tipped scribe making for a very durable part. This is especially useful for replacement parts on guns as the finish can be closely matched to the older period parts in color and finish making repairs almost completely indistinguishable from the original part or an original replacement part. And, while the long bow defeated the chainmail armor, the crossbow defeated plate armor rendering the “Knight in Shining Armor” just another casualty on the field of battle … and at the hands of a mere commoner no less.
Bill Bullock i don’t feel worthy after reading what you just outlined, but as a teen a friend and I discovered a crude form of case hardening heating mild steel blades in a wood fire until it reached a glow. Presumably it soaked carbon from the charcoal into it’s surface. A carbon bath like that might have quite a toughening effect on low carbon steel plate.
This is all true, yet it did not prevent both infantry and mainly cavalry, during the advent of firearms continuing to wear Cuirass armour:
http://en.wikipedia.org/wiki/Cuirass
The is also picture of German infantry armour from 1916, so this reference is relating to bulk of discussion.
I believe I read somewhere in a french gun mag that the germans converted captured chauchats to 8mm mauser hence the straight mag
If the “Sho-Sho” in question were the U.S. .30 caliber version, a new 7.9 x 57 barrel might be the only change needed. The U.S. .30 cal (7.62 x 63) magazine could easily accommodate the 7.9 round. Or a modified version of the 20-round non-detachable “sniper” magazine for the Gew 98 could have been used.
Modifying the 8mm Lebel chambered version would be more of a challenge due to its different bolt head, plus the magazine interface for the wacky “crescent-moon” magazine needed for the fatter and more tapered 8 x 50R cartridge.
I could see such a mod being carried out in the time frame of the photograph (1918), because by then the German Army was desperate for light machine guns of any kind, notably for their assault troops in anticipation of the 1919 offensive (that was abruptly rendered irrelevant by the Armistice).
Although considering their poor record of reliability and safety in both 8mm and 0.30in, I wouldn’t expect “Sho-Sho”s rebarreled to 7.9 to last more than a couple of magazines’ worth of full-auto fire before something…broke. My money would be on a fractured receiver.
cheers
eon
The 8x50R mm Lebel always made me wonder…. with that high taper and head diameter, it must have necessitated correspondingly thick chamber wall and thus bulk of weapon across chamber area.
It does not look to me as very smart to begin with, although one has to consider that Lebel was actually the first with this type of ‘semi-modern’ shot and besides, the taper must have been beneficial at extraction.
Hopefully not parting with the subject, it may be perhaps useful to mention that combination of Nickel and Silicon had been ‘true & tried’ in application such as inner lining of combustion engines cylinders; they produce hard wearing surfaces:
http://en.wikipedia.org/wiki/Nikasil
This had been apparently overcome lately by new and advanced methods such as cylinder ceramic lining, pioneered by Japanese motorcycle builders. We are getting back to ceramics pretty quickly :-))))
Lemme tell ya guys, I hand forged an axe blade from an old Chevy truck spring piece under the guidance and supervision of a black smith… I’m no metalurgist, but that is some gnarly, hard steel! I’m not sure my hands’ve recovered from pounding on that thing…
Tassiebush, you are not only an inventor, but a genius as well! In your teens you and a friend accidentally discovered (or at the very least re-discovered) one of the most important advancements in the history of metallurgy. The progression was that early weapons were made of copper because it was often found in relatively pure form. Then they went up against a tremendous advancement of mixing natural tin with copper and making bronze. The newer technological weapons cut the blades of the copper swords clean off. Later the bronze swords went up against the first iron swords with the same results. Next probably came carbonized iron of “case hardened” metal … same result but wider application. Then steel leading to the more modern technologies. A prime example of these accidental advances was the Bowie Knife which reportedly had a small meteorite melted into the steel making it into a form of nickel-steel. I believe this because according to my grandfather, who was supposed to have been distantly related to the smith who made it, this person had discovered several small meteor fragments and had learned their benefits. Proceed from there to modern steels without which modern weapons could not exist. This covers your claim to the title of “Inventor.” The title of “genius” comes from the fact that you and your friend were able to recognize that this process produced an advanced blade … the recognition of advantage. And what you did with an open fire and charcoal in your teens is in essence exactly what I do now with my more advanced machinery (a.k.a. “Toys”). Most of the inventions I have made have been the results of accidents that I followed for years.
An appreciative remark, to be sure… I believe Tassiebush shall be rightly delighted.
Regarding early workings on iron swords, it came to attention of crafty humans that, if hot sword blade was quenched into horse urine (oh boy, what a smell…), it would produce both toughness and hardness of edge. Hence came “carbo-nitriding” in modern terms. It’s actually funny how people ‘discovered’ many new qualities of their implements, accidentally.
Denny & Dave Carlson: Denny first; the ceramic cylinder liners are a MAJOR advancement in combustion designs. Ceramic top-plate pistons are another. In fact, we are probably poised on the brink of tremendous changes in combustion designs including weapons. For instance, envision a rifle with a muzzle velocity of 5,000 fps/~1525 mps. Oops, that harkens back to WWII era impulse technology associated with their Rocket Bullet research. The ceramic technology would also solve a MAJOR problem with caseless ammunition; the fact that the cases remove an appreciable amount of the thermal production from the system; i.e. they get hot when the weapon is fired and then are ejected along with the excess heat. If the interior surface of the chamber and barrel could be coated with a ceramic metal you described it would emulate out former developments of interior ceramic coatings of the exhaust manifold and exhausts of race cars. This not only keeps the manifolds cool but also conserved heat/power to drive the turbochargers, reduces the temperature of the engine compartment and the cockpit (lots of personal experience with the last). Dave Carlson: leaf-springs from both automobiles and trucks are a tremendous source of metal for knife blades as are old files and sawmill blades of yore! They make great arrow points as well. In my dark past we first made the prods (bows) for our crossbows from pickup truck springs. Some we cut down for lower power prods but the really BIG BOYS used the un-cut springs for a 400-1200 pound pull prod. These we equipped with hand wenches (windless) to cock them and shot solid steel bolts (arrows). These would completely pass through a very large bear or a Plains Bison. With the appropriate tempering they make first-class knife and hatchet/tomahawk blades. But they do not measure up to the Japanese Samurai Swords the metallurgy of which we are yet to reproduce or completely understand. This last lest we indulge in some form of superiority character based upon our “advanced” technology. As for passed-up technology from the past I would nominate Dr. Gerald V. Bull and Project HARP. Also, apologies for any off-topic material and my verbosity on such matters … I do get carried away sometimes.
Very true, Bill.
My only reservation, mostly due to my shabby understanding of many important details is, that ceramic layer needs metal backing. On particular gun application such as 25-30x– mm auto-cannon this might work extremely well. But then again, how those two materials are going to cooperate in long term?
What seem to make them work in combustion engine is that the contact area is large and layer is thin… well saying that, it may be in some way transferred into barrel. Maybe same way the hard-chrome plate layer is deposited. Bingo!
APPROACHES FOR THE DESIGN OF CERAMIC GUN BARRELS
Ryan Emerson, Robert Kaste, Robert Carter, Larry Burton*, Jeff Swab U.S. Army Research Laboratory Weapons & Materials Research Directorate AMSRD-ARL-WM-MB Aberdeen Proving Ground, MD 21005-5069
APPROACHES FOR THE DESIGN OF CERAMIC GUN BARRELS
Ryan Emerson, Robert Kaste, Robert Carter, Larry Burton*, Jeff Swab U.S. Army Research Laboratory Weapons & Materials Research Directorate AMSRD-ARL-WM-MB Aberdeen Proving Ground, MD 21005-5069
Stormtroop Tactics, Innovation in the German Army, 1914-1918 by Bruce I. Gudmundsson is an well referenced and excellent reference on the evolution of the Hauptman Rohr’s ideas and the Sturmtrupp.
Also reference Ceracote Ceramic Coatings’ Dyna-Bore Coat (DBC) and Otis LifeLiner. These are outgrowths of the search for a ceramic coating of the interior surface of predominately military gun barrels with civilian applications. They are presently mostly directed toward artillery pieces. I personally lean toward a smooth-bore/Paradox barrel with RAP/RPP (Rocket Assisted Projectiles/Rocket Propelled Projectiles) that incorporate Base Bleed Technologies as well as innovative propulsion dynamics. So far this has increased the effective range of field artillery by at least 30-55% with no other alterations of the field piece. This once again nears the technology espoused by Dr. Bull.
Mr.s Cherndog and Pdb: I thought you got the memo; since God invented Marines he no longer has to bother with humankind’s battles! They take care of the detail work for him! Simper Fi!
Oops, totally forgot about that. Thanks for the update!
This is really worth remembering. But I want to know what steel to make the gun at that time. We Songshun steel company want to know.