Today I am chatting with Paul Levy of Brownells about their BRN-180 upper; a modernization of the original Armalite AR-180. This particular project is an interesting combination of recreating an older design but simultaneously modernizing it – so let’s pick Paul’s brain about some of the unexpected hurdles that came up! Thanks to RIA for hosting us.
Related Articles
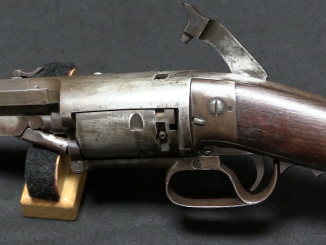
Percussion
North & Skinner Wedge-Lock Revolving Rifle
This rifle is lot #1237 in the upcoming May 2019 Rock Island auction. Patented in 1852 by Henry North and Chaucey Skinner, about 700 of these revolving rifles were made by 1856. The design used […]
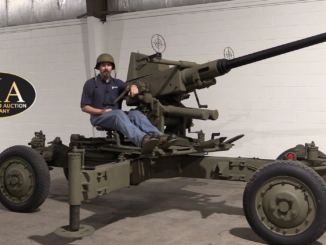
Artillery
Swedish Antiaircraft Artillery: Bofors 40mm Automatic Gun M1
Note: In the video I mistakenly describe this as a two-stamp NFA gun. It is actually deactivated, and thus does not require a tax stamp. Sorry for the mistake! RIA’s catalog page for this cannon […]

Light MGs
Online-Only Auction at RIA
It is worth pointing out the RIA has added a third type of auction in the last year or so; online-only. The idea is to have a lower-overhead way to sell some of the things […]
Since they moved away from an exact reproduction anyway, I’d love to see them engineer trunnions that could take AR-15 barrels, coupled with clamp-on gas blocks.
Does it have a folding stock? Back in the day the AR 180 was prefered by the people who wanted a folding stock.
That was the biggest choise.
In the movie Stingray, (not a good movie) but it was filmed in my home town. It had a AR 180 in the bar seen. The rifle belonged to a friend of mine. Don Page. That was the first time I was exposed to a autosear.
What a neat gadget.Ion should do a story on those as well.
AR-160 FTW!
Just in case anyone’s interested, Nodak Spud makes a lower that fits this upper (& other AR15 uppers) that is AR180-esque. https://www.nodakspud.com/NDS-1815.htm I built one of these with Brownell’s upper & a MagPul MOE Rifle stock. It’s sort of what an AR180 would look like if it were still in production. Brownell’s makes a 180-ish lower that has a rail on the receiver tower to accept rail mount folding stocks if you can’t live without this feature https://www.brownells.com/rifle-parts/receiver-parts/receivers/lower-receivers/brn-180-stripped-lower-receiver-forged-prod130438.aspx?psize=96 .
I can do without an obvious sales pitch
In my opinion, this does not in any way attract “reproduction”.
This is another Frankengun for the M16 using some parts of the AR18.
If the guys managed to get this to work reliably enough, well done.
But if you position it as “innovation”, then every next Chinese plastic butt comb will pass for a “technical breakthrough.”
How many of them have already been, all sorts of Paraius and others?
One more nothing.
friends:
way back way way back i bought an ar-180b from armalite. interesting rifle, great & clever design, but armalite’s version was betrayed by shoddy construction, inadequate material strength, and a company that did absolutely nothing to redress complaints and warranty issues.
where to begin?–
the metal for the upper receiver was not of sufficient strength and thickness. it was so thin that welds on the bottom simply burned through the metal of the receiver, and the receiver cracked, e.g., “broke”, at the seam between the weld and the sheet metal. (it was “sheet metal,” and not metal plate. there is a difference.)
i complained of this to armalite. nary a peep in reply, ever.
in spite of all this the rifle worked. but, my long term expectations that this could continue were nil, so i sold it.
too bad. if they had made the upper from 10 or even 11 gauge steel, it would have had more than enough strength, and could have been machine welded pretty easily. but, they did not, ever, to the best of my knowledge.
i hope that the new “purveyors” of the rifle have done better in this regard. there is a reason why the ar-18 is the basis for many gun designs around the world, … , it is a solid concept.
p.s. how do i come by these opinions?– grandpa’s, father, older brothers, welders, mechanics and blacksmith. i have worked in a metal shop doing metal fabrication on a very large sheer press, automated band saw, and the like. i am no expert, but i have been around metal fabrication a great deal. that’s how. and, i know when a weld is too hot for the surrounding metal, and simply consumes it by heat. ‘nuf said.
They (Armalite) made the same mistake as with AK47. They tried to organize the functioning of automation with complex kinematics and dynamics through simple technological solutions.
It’s kind of like trying to build a space telescope out of bottle donuts, bamboo stalks and ropes.
Each detail individually seems simple and functional. But as soon as you try to put together more than two of these parts, it turns out that things are not easy.
“Suddenly” it turns out that the accuracy of each part must be at least a class higher than that provided by stamping. And the assembly personnel must be of the appropriate level of training.To understand what exactly they are doing, and not to stick a stick in a hole and press a button like a trained monkey.
All together, it leads to the fact that with relatively small volumes of production, the product either becomes too expensive, or it will be of high quality like any other monkey’s crafts.
Any already existing structure was designed for a specific production, with its own equipment, personnel and other means.
And trying, for example, to stamp something that was designed for casting, as well as milling something designed for stamping…
It’s not even funny.
The AK was certainly no mistake, but a tremendous success.
I have entertained the idea of a Brownell BRN-180S pistol upper. I did buy an FM Products AR-180 type upper, gas operators (DIGS) whereas the BRN180 is a piston operated upper. I haven’t shot it yet but look forward to doing so soon.